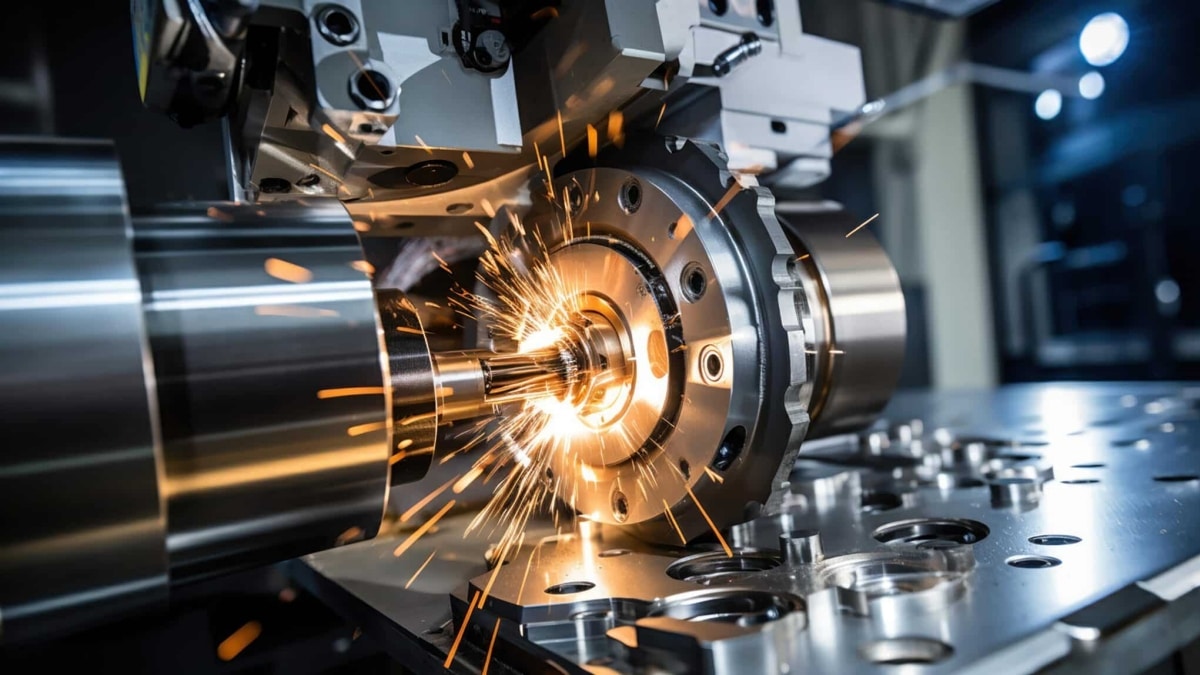
5 CNC Machining & Automation Capabilities
CNC machining and automation have revolutionized the manufacturing industry, offering improved efficiency, precision, and scalability. With rapidly advancing technologies, businesses are continuously exploring innovative ways to leverage CNC machining for various applications. Below, we’ll explore five key CNC machining and automation capabilities that make them indispensable in modern manufacturing environments.
Benefits Of CNC Machining
1. Unmatched Precision and Accuracy
CNC machining stands out for its ability to deliver exceptional precision and consistency. Using computer-controlled systems, these machines can produce parts and components with exacting accuracy, often achieving tolerances within mere microns. This level of precision is critical in industries like aerospace, automotive, and medical device manufacturing, where even the smallest deviation can compromise safety or performance.
The integration of automation further enhances this precision. With advanced sensors and quality assurance mechanisms, automated CNC systems can monitor every step of production, instantly detecting and correcting errors. This ensures uniformity across large production runs, minimizes waste, and guarantees consistently high-quality results. By seamlessly combining precision with automation, CNC machining not only meets rigorous industry standards but also reduces production costs, making it an invaluable tool for modern manufacturing.
2. Multi-Axis Machining for Complex Geometries
Traditional machining methods often fall short when it comes to creating intricate parts or components with complex geometries. CNC machines, particularly those equipped with multi-axis functionality, excel in this domain. With 3-axis, 4-axis, and even 5-axis machining, manufacturers can produce sophisticated designs without requiring multiple setups or extensive manual intervention.
These advanced machines can handle complex curves, angles, and cuts with ease, which is particularly advantageous for industries like robotics, consumer electronics, and energy production. Automation further augments multi-axis machining by streamlining the programming process and allowing for continuous operation. For example, automated toolpath optimization minimizes cycle times while maintaining accuracy, enabling high-volume production of intricate parts.
3. Scalability in Production
CNC machining and automation are ideal for scaling production, whether it’s a limited prototype run or full-scale manufacturing. CNC technology adapts effortlessly to varying production needs, allowing businesses to modify designs or adjust production volumes without significant delays or disruptions.
The integration of automation takes scalability a step further by enabling 24/7 operation with minimal supervision. Robotic loaders, automated tool changers, and IoT-enabled monitoring systems facilitate continuous production, ensuring deadlines are met without sacrificing quality. This capability supports industries that demand responsiveness and flexibility, such as consumer goods, construction, and telecommunications, providing a competitive edge in fast-paced markets.
4. Enhanced Material Versatility
CNC machining is renowned for its ability to work with a broad range of materials, from metals like aluminum, titanium, and stainless steel to plastics, composites, and even wood. This versatility gives manufacturers the freedom to choose materials based on specific project requirements, such as durability, weight, or aesthetic appeal.
Automation complements this versatility by optimizing workflows for different materials. For example, automated CNC systems can adjust cutting speeds, tool types, and other parameters dynamically to accommodate different material properties, reducing downtime during material switching. This capability ensures that manufacturers can efficiently handle diverse projects, making CNC machining a go-to solution for sectors such as industrial machinery, marine, and electronics.
5. Seamless Integration with Digital Technology
The future of CNC machining lies in its seamless integration with digital technologies, commonly referred to as Industry 4.0. Modern CNC systems come equipped with IoT connectivity, advanced sensors, and software-driven controls that enable real-time monitoring and data analysis. This digital transformation empowers manufacturers to make informed decisions, anticipate maintenance needs, and enhance productivity.
Automation further amplifies these benefits by reducing manual dependency, improving safety, and ensuring consistency across all production steps. For instance, smart automation systems can predict tool wear, schedule preventative maintenance, and even autonomously reroute production processes to avoid downtime. The combination of CNC machining and digital automation creates a highly efficient and interconnected manufacturing ecosystem, paving the way for increased profitability and sustainable operations.
Does My Company Need CNC Machining?
When determining if CNC machining is right for your company, it’s important to evaluate factors like production volume, part complexity, and quality requirements. CNC machining excels at producing intricate and precise components with tight tolerances, making it ideal for industries such as aerospace, medical, automotive, and electronics. If your business relies on consistent quality and scalability, CNC machining can offer significant advantages by reducing human error and ensuring uniformity across batches. Additionally, consider the potential cost savings from minimized waste and improved production speed. Investing in CNC technology can be a game-changer for businesses looking to innovate and maintain a competitive edge.
The Role of CNC Machining in Metal Fabrication
Metal fabrication is a core application area where CNC machining truly shines. By leveraging computer-controlled precision, CNC machines can cut, shape, and form metal into highly intricate designs that manual methods struggle to achieve. This makes them indispensable for producing custom parts, prototypes, and large-scale assemblies in industries like construction, energy, and transportation. CNC machining enhances metal fabrication processes by delivering unparalleled accuracy and repeatability while handling materials ranging from aluminum and steel to titanium and exotic alloys. The automation provided by CNC technology also reduces lead times and labor costs, enabling manufacturers to meet tight deadlines without compromising quality. For companies operating in metalworking, integrating CNC machining can streamline production workflows and unlock new possibilities for innovation and efficiency.
Adopting these advanced capabilities will not only future-proof your manufacturing processes but also position your company as a leader in the evolving industrial landscape.